Seasonal Care Tips for Wooden Flooring (Summer vs. Winter)
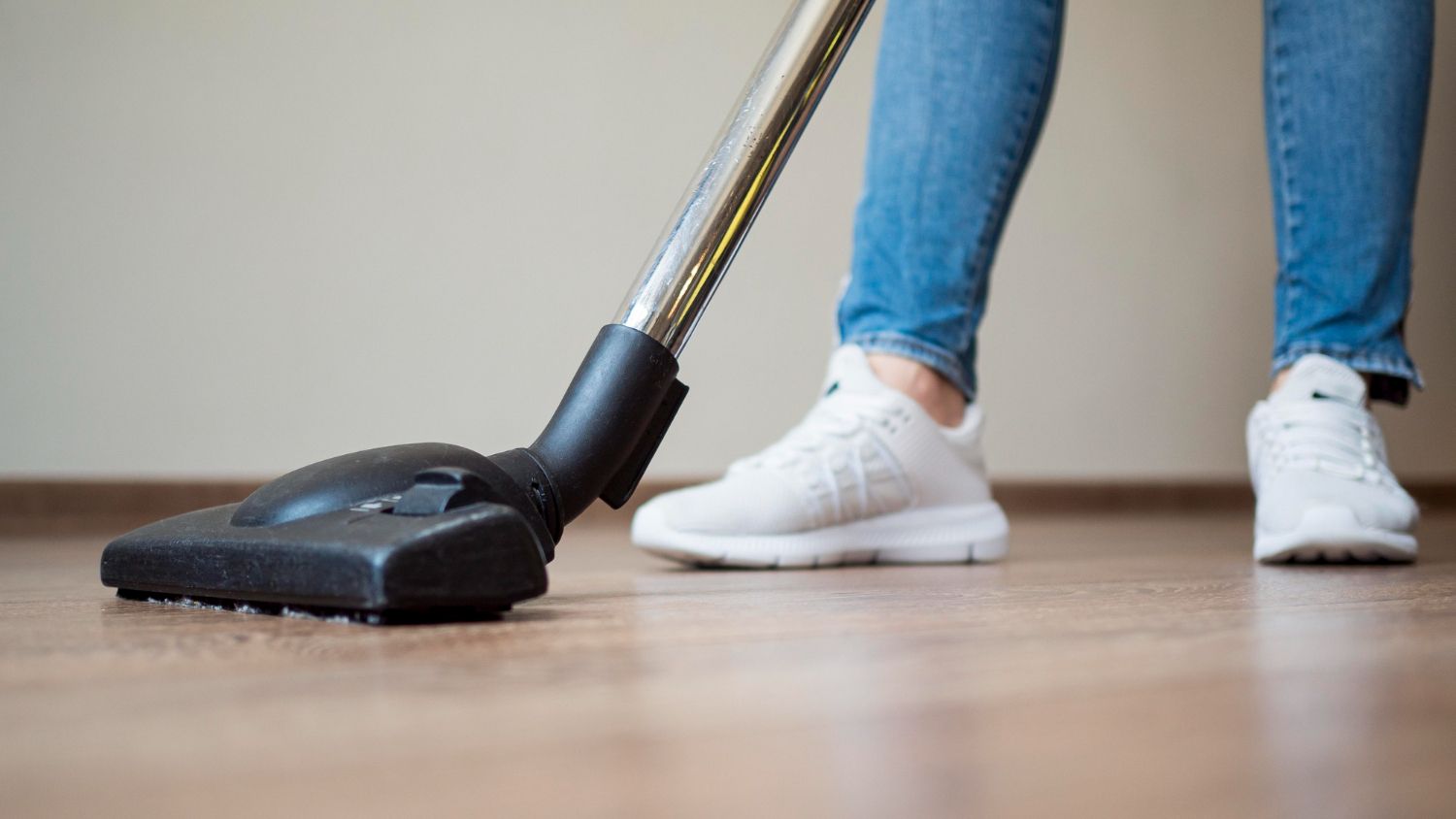
Wood flooring undergoes profound physical transformations as seasons shift, responding to humidity and temperature fluctuations with microscopic movements that cumulatively impact structural integrity. Understanding these material responses allows homeowners to implement targeted care protocols that prevent common seasonal damage—from summer’s swelling-induced cupping to winter’s dryness-triggered gaps. This guide distills scientific principles into actionable maintenance practices.
The Mechanics of Seasonal Wood Movement
Wood’s hygroscopic nature drives its reactive behavior. Summer humidity (typically 60-80% RH) causes cellulose fibers to absorb atmospheric moisture, leading to lateral expansion. Winter’s arid indoor air (often 15-35% RH) forces moisture release, resulting in contraction. Tangential-cut boards exhibit 2x greater movement than quarter-sawn planks. These dynamics necessitate divergent seasonal approaches to avoid permanent deformation or adhesive failure.
Summer-Specific Threats and Mitigation
High humidity poses the greatest summer risk. As planks absorb excess moisture, compressive stress causes edge cupping or center crowning. UV exposure simultaneously degrades finishes and bleaches wood pigments. Engineered floors face delamination risks when veneers and core layers expand at differing rates.
Critical Humidity Control Protocol
Maintain 45-55% relative humidity using whole-house dehumidifiers. Position standalone units in basements where moisture accumulates. Enhance cross-ventilation by opening opposing windows during cooler morning/evening hours. Place silica gel desiccant trays near exterior doors to capture incoming humidity. Avoid wet mopping—opt for microfiber damp mops with pH-neutral cleaners to prevent surface swelling.
UV Defense Tactics
Install low-E window films blocking 99% of UV radiation. Rotate area rugs weekly to prevent differential fading. Apply water-based polyurethane with UV inhibitors every 3 years. Close blinds during peak sunlight hours (10 AM–2 PM) to minimize photo-oxidation in vulnerable species like cherry or Brazilian walnut.
Winter-Specific Challenges and Solutions
Dry winter air shrinks wood, creating gaps between planks exceeding 3mm—a tripping hazard and debris trap. Subfloor heating exacerbates moisture loss, causing end-grain cracking in solid wood. Abrasive contaminants like de-icing salts accelerate finish wear while lowering indoor humidity below 30% risks structural checks.
Humidity Optimization Methods
Operate furnace-mounted humidifiers maintaining 35-45% RH. Bypass models prevent "white dust" mineral deposits. Perform weekly damp mopping with distilled water (300ml per 10m²) using wrung-out microfiber pads. For gaps wider than 5mm, inject epoxy-sawdust slurry after professional assessment.
Abrasion and Contaminant Defense
Deploy commercial walk-off mats at all entries, capturing 85% of destructive particulates. Clean floors biweekly with neutral cleaners—never vinegar or ammonia-based solutions. Apply temporary paste wax coatings before winter; their sacrificial layer protects against salt corrosion. Place felt pads under furniture legs to prevent localized compression damage during rearrangement.
Essential Seasonal Transition Checklists
Spring Preparation for Summer
- Service HVAC systems and clean dehumidifier coils
- Verify 10mm perimeter expansion gaps
- Apply protective refresher coats to high-traffic zones
- Trim vegetation to improve subfloor ventilation
Fall Preparation for Winter
- Calibrate humidifiers and install hygrometers
- Seal gaps between baseboards and flooring
- Test radiant heating systems for hot spots
- Install walk-off mats at exterior entries
Material-Specific Considerations
- Engineered Wood: Requires tighter humidity control (40-50% RH) to prevent core-veneer separation. Avoid steam cleaning which penetrates seam vulnerabilities.
- Solid Hardwood: More prone to gapping; use professional gap-filling techniques when separations exceed 4mm.
- Bamboo: Susceptible to fiber splitting below 30% RH; requires vigilant humidification.
- Reclaimed Timber: Higher movement tolerance but needs bi-annual finish reinforcement.
Professional Intervention Indicators
Recurring cupping suggests subfloor moisture intrusion requiring hydraulic diagnostics. Cross-grain cracks indicate structural shifts needing assessment. Persistent squeaking reveals subfloor detachment. Buckling exceeding 8mm lift demands board replacement. NWFA-certified technicians use non-invasive moisture mapping to identify hidden issues before catastrophic failure.
Long-Term Preservation Framework
Install smart climate systems like Ecobee that auto-adjust humidity. Use breathable natural fiber rugs (jute/wool) instead of vinyl-backed mats. Every 3-5 years, lightly screen and recoat surfaces to maintain moisture barriers. Document seasonal changes through photogrammetry—annual overhead photos reveal subtle movement patterns requiring intervention.